Your brake and shift cables connect you to your brakes and derailleurs, and are what you use to tell you brakes and derailleurs what you want them to do. Most cables are open to contamination especially in wet conditions. Cables that are rusty, dirty, or clogged with the wrong lubricant can disrupt the connection between you and your brakes and derailleurs, and can make even the best braking and shifting systems work inconsistently or not at all. In this video we demonstrate in three easy steps how to cut, trim, and lubricate your cables to ensure precise reliable braking and shifting that will remain consistent through any condition. Depending on what you're trying to do, you'll need brake housing, brake wire, and metal end caps, also known as ferrules, to put on the ends of the housing, as well as shift housing, shift wire, and metal or plastic ferrules, depending on the diameter of your shift housing. You will also need a good set of shear cutters, a tool with a sharp point, in this case a sharpened spoke, and Finish Line Extreme Fluoro- fully fluorinated, low viscosity, lightweight grease.
Step One: knowing your cables. Braking shift cables differ from one another in a couple of ways. They both comprise two parts in outer covering called housing and an inner wire that's inserted into the housing. Brake housing consists of a long, coiled strip of wire that's protected from moisture by a plastic outter sleave. Most modern brake housing also contains a plastic inner liner to reduce friction between the housing and the inner wire. In the past, before index shifting provided us with the clicks we all know, brake housing was used for both brakes and shifters. By contrast, shift housing is designed for stiffness in response to the demands of index shifting systems that won't shift precisely with flexible brake housing. Stiffness is the result of long strands of wire that run parallel to the length of the housing, instead of being coiled into a spiral. Like brake housing, shift housing is protected by a plastic sleeve and often contains an inner liner. However, you should never use shift housing on your brakes, because it can burst under the high loads of braking.
Next up is the inner wire. Here again we see a difference between brake and shift cables. In fact, brake inner wire actually comes in two varieties: one for road bike brake levers and one for mountain bike brake levers. The two differ in respect to the small metal head that's found at one end of the wire. Some cable manufacturers actually sell wire that has a road head at one end and a mountain head at the other, allowing you to clip off the head you don't need. Installing the inner wire into your brake levers is perhaps the easiest step in installing cable. In the case of road wire, when you pull on your brake lever and look inside, you'll see a small part with a specially machined hole in it. Simply insert the end of the wire without the head through that whole and continue pulling the wire through the lever, either from the back in the case of levers like this Shimano STI lever, or out the top in the case of some older levers. Once you pull the wire all the way through, use your fingers to seat the head of the wire into that specially machined hole and let go of the lever to close it. Don't worry if the head doesn't stay seated, you will have plenty of opportunity to make sure it is seated before you finish installing the cable.
Installing the inner wire into a mountain bike brake lever is very similar, maybe even easier. Mountain bike brake levers have a opening for the head of the wire on the outside of the body, usually on the underside of the lever. The body also has a slot in it as does the knurled insert that threads into the body and allows you to adjust the cable later and the lock ring that holds that insert in place. To install the inner wire, first line up the slots, then insert the head of the wire into the opening in the lever body. Once you've done that, guide the wire into the slots and last of all, rotate the insert, the lockring, or both so that the slots are no longer lined up. This will keep the wire from falling back out as you complete the installation.
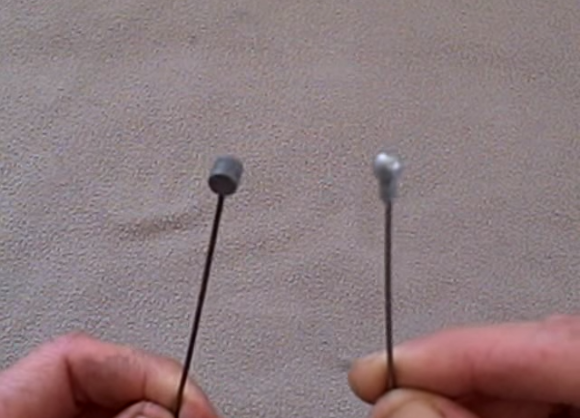
Mountain Bike vs Road Bike Cable Head
Shift wire is the same for road and mountain bike shifters. Both cases have a small cylindrical head at the end of the wire that fits into a special machine hole in the shifter. On this Shimano STI lever, you insert the end of the wire without the head into the side of the shifter, then pull it out the other side, and seat the head like you did with the brake wire. If the wire won't go in, check to make sure that the shifter has shifted all the way down to the smallest cog, if it's a rear shifter, or the smallest chainring, if it's a front shifter. Insert the wire into a mountain bike shifter the same way. First check to make sure that the shifter is shifted to the lowest position for the smallest cog or the smallest chainring, and then run the wire through, seating the head of the wire into the shifter with your fingers when you're done.
Step 2: cutting the housing. This is where the right set of cutters can make your life a lot easier. Cutting brake housing is actually very easy. Once you correctly sized the housing, place it in between the jaws of the cutter and squeeze. The excess housing will come right off. However, if you look closely, you might notice that the metal coil was cut right in the middle, leaving a spur of metal sticking out of the housing, or that the inner liner was deformed as you made your cut, obstructing the opening of the housing and the path of the inner wire. In this case, you might need to cut the housing again slightly further down where the coil cuts cleanly or even use a rotary tool with a cutting disc, like a dremel, to remove the spur. Once you have a clean-cut, insert the pointed tool into the inner liner and widen the opening so that the inner wire can pass through without obstruction. Shift housing cuts the same way. You'll recall that shift housing is straight, not coiled, so there's no problem with spurs, however cutting flattens the opening a lot more than it does with brake housing, so you need to take more care to widen the opening. Sometimes it even helps to pinch the outer plastic sleeve back into shape.

Cut Housing with Tool
Step 3: lubricating the housing. Some mechanics don't lube cables because they believe that the inner liner of the housing is slick enough and that lube will only cause drag and slow the inner wire down. However, because it's fully fluorinated with a higher lubricity than teflon, Finish Line Extreme Flouro is slicker than the inner liner and its low viscosity guarantees that the wire will move in the housing without any drag. It also provides protection against corrosion for the life of the cable, a large part of why you lubed them in the first place. To apply it simply insert the tip of the syringe into the opening where you'll be inserting the inner wire and squeeze. You don't need much and once you see grease beginning to come out you're done. Then take a metal ferrule and place it over the end of the housing pushing it down so that it's as tight as possible. If you'd like you can place the ferrule between the jaws of your cutter and gently squeeze. This is called crimping, and leaves and indentation that helps hold the ferrule in place. Once you've done that, all that's left to do is insert the inner wire into the housing. As you do so, the wire will distribute the grease along the length of the housing. Shift housing is lubricated the same way as break housing. Take your Finish Line Extreme Flouro, insert the tip of the syringe into the open end of the housing, and squeeze until you see grease begin to come out around the tip. Then, if using five-millimeter shift housing, which is the same diameter as brake housing, take a metal ferrule, place on the end of the housing, and run the inner wire through. Many modern shift systems use four millimeter housing, which is slightly narrower. The only difference here is that once you've lubricated the housing, you place a narrower plastic ferrule plastic on the end. It's usually already crimped. The two sizes are actually interchangeable and many mechanics prefer to use five-millimeter housing for added stiffness.
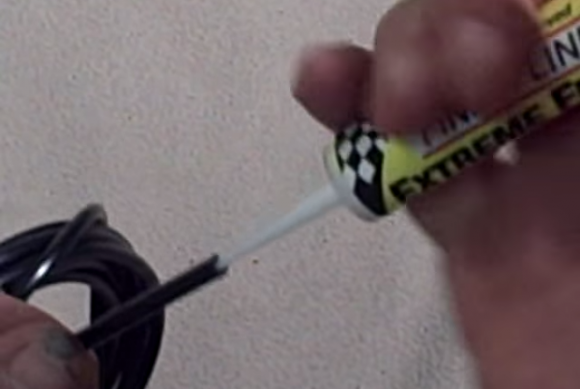
Squeeze Lube into Housing